
WHY IS THE CONSTRUCTION METHOD SO IMPORTANT?
When it comes to pod/enclosure construction, there are a few key elements that are paramount to the overall sound, fit, and finish. These elements include rigidity, density, design flexibility, and longevity.
What does this mean?
​
Density and rigidity go hand in hand but are not one in the same. You can have an incredibly rigid component that isn't very dense or an incredibly dense component that isn't very rigid. Our fabricated parts are made with materials such as basalt, fiberglass, billet alloy, acrylic, and foamed PVC, which, when applied correctly, offer the maximum in both worlds.
​
Bespoke design and seamless integration are a large part of what we do. The ability to create any shape imaginable while retaining incredible strength and sonic performance makes our material choice and fabrication processes vastly superior.
Many other stores use conventional materials to manufacture parts like MDF, timber, and body filler. There's no question that the use of these materials in this application is subpar and subject to premature failure, along with inferior physical and audible characteristics. We are so confident in our fabricated parts that we offer a lifetime warranty.
HOW DO WE BUILD ENCLOSURES?
Although these processes change from part to part, we can help to give you more of an understanding of how we create parts with a step-by-step overview. We use these procedures for door pods, stand-alone enclosures, built-in enclosures or even one-off panels and covers. The process for creating pillar pods and sail pods is slighly different but the same in most regards.
ENCLOSURE MODELING
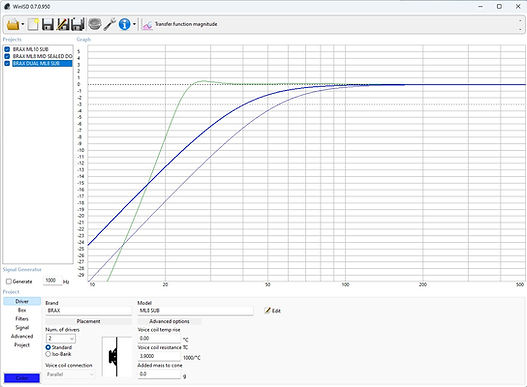
In the early stages of the build design, we start with driver modelling to ensure that it not only looks great and fits within the clients aesthetic requirements but also reaches our performance metrics. We pay particular attention to things such as sensitivity and power requirements, frequency response, phase response and group delay. It's also a great way to compare different components and pieces of equipment as we can compare different drivers and the relationship they will have with the acoustic environment

STEP BY STEP - FRONT SUB
Whilst this may not be a conventional enclosure it sure is an epic one. Why not pick something interesting to walk you through the process?​
Front subs are brilliant for mid-bass reinforcement and vastly improve the bottom end performance of the front stage. They are a game changer when it comes to the ultimate sound quality.

CHECKING CLEARANCE
Step one is always making sure you can pull off the task. Whether it be, checking clearances, finding fixing points or establishing a way to fabricate a difficult part.
PREP
Extensive prep work is carried out to ensure your vehicle is protected. Next, we apply a very thick layer of tape to the area we want to glass. We try to avoid any wrinkles in the tape as this means less sanding in the future as this now becomes our mould.
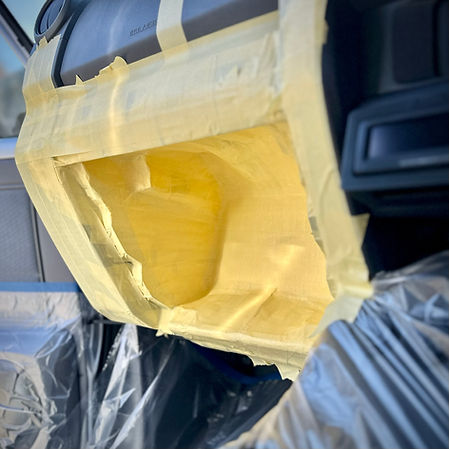
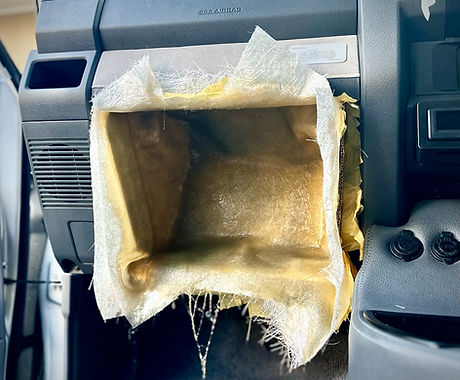
FIRST LAYERS
Although this isn't a particularly attractive step it certainly is an important one. Two layers of 450gsm fiberglass are laminated and left to cure. Once cured the part is removed from the dash and prepped to receive 10 more layers, laminating to 14mm thick.
BAFFLE
In the background we've taken a mould of the glovebox lid, laminating 3 layers of custom made 950gsm basalt weave. The acrylic mounting ring was then bonded with structural epoxy and 10 layers of 450gsm fiberglass laminated to the desired baffle shape.

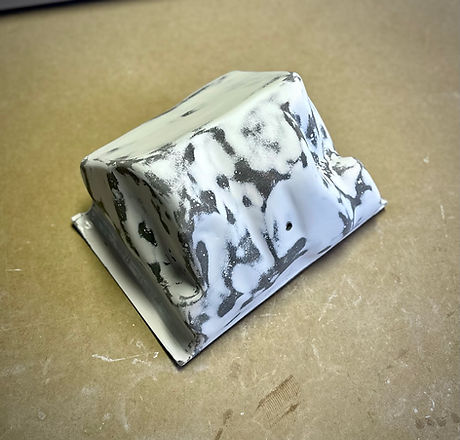
BONDING TOGETHER
A few steps have now taken place. The basalt baffle has been bonded to the body with a 25mm bead of structural epoxy, creating a sealed enclosure. The whole structure has also been flow coated in and out then sanded to a paintable finish.
FINISHINGS
We always make sure our pods and enclosures are finished on every surface; this is no exception. This enclosure was sprayed and left to cure.


UPHOLSTERY
All our upholstery is done in house to our standards. we have access to a wide range of materials such as Alcantara, Macro suede, leather and a range of durable vinyl. This enclosure was upholstered in custom matched vinyl.
ISOLATION
Being that we are mounting hard up to multiple hard surfaces, isolation material is a must to prevent resonances. This material was installed in key areas.
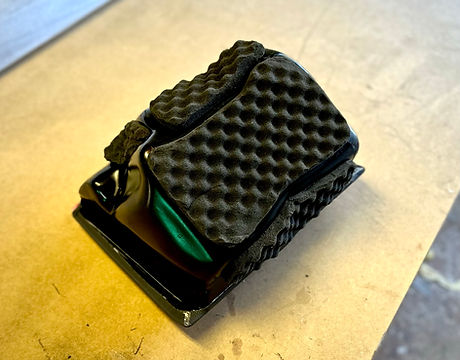

LETS TRY A DIFFERENT PROCESS
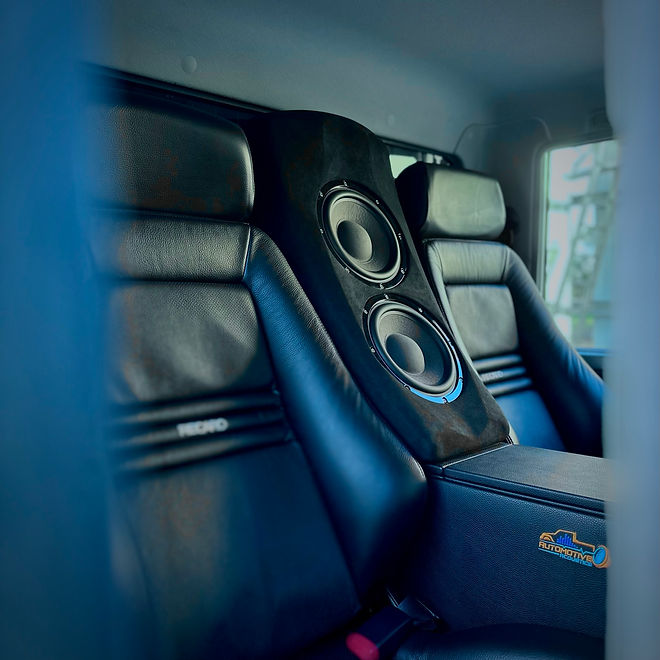
STEP BY STEP - STAND ALONE ENCLOSURE
Lets explore a slightly different process, where we employ foam to create our plug.
FOAM PLUG
This process starts with a foam block. Once we have rough cut our block to the approximate outer dimensions we can begin to shape the foam, test fitting along the way. Once happy, we then insert the acrylic mounting rings to be laminated in.


LET'S LAMINATE
As we have test fitted our plug, making sure we've allowed clearance for the desired wall thickness and upholstery thickness, we begin to laminate the fiberglass directly over the foam.
In the spirit of keeping things short, a few steps have now taken place. The enclosure has been laminated to a wall thickness of 14mm and has been sanded. Once these steps have been completed, we remove the foam to reveal a single piece, hollow structure. The inside is then coated with a gelcoat layer.
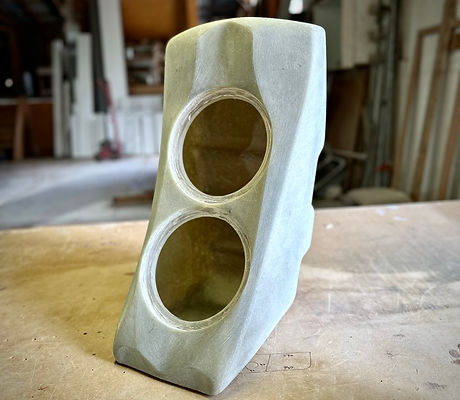
REMOVING THE FOAM

UPHOLSTERY
Now that the gelcoat has cured, we can begin the upholstery process. This client opted for black Alcantara to match the rest of the build.
CABINET DAMPENING
We take this opportunity to install our high-level cable and install the genuine sheep wool cabinet dampening. we use sheeps wool for its superior sonic characteristics.


INSTALL DRIVERS
It's time to install the drivers. We drill and tap the holes for the mounting bolts and install the necessary gaskets.

These techniques allow us to do away with body fillers, "milkshakes" and conventional construction materials. Unlike conventional methods, our parts become a single structure thus greatly improving the overall strength and rigidity of the part. Other benefits include increased manufacturing efficiency and an approach that simply cannot be done with traditional materials.
​
Quality is our standard and not an opinion. We guarantee your investment to last.